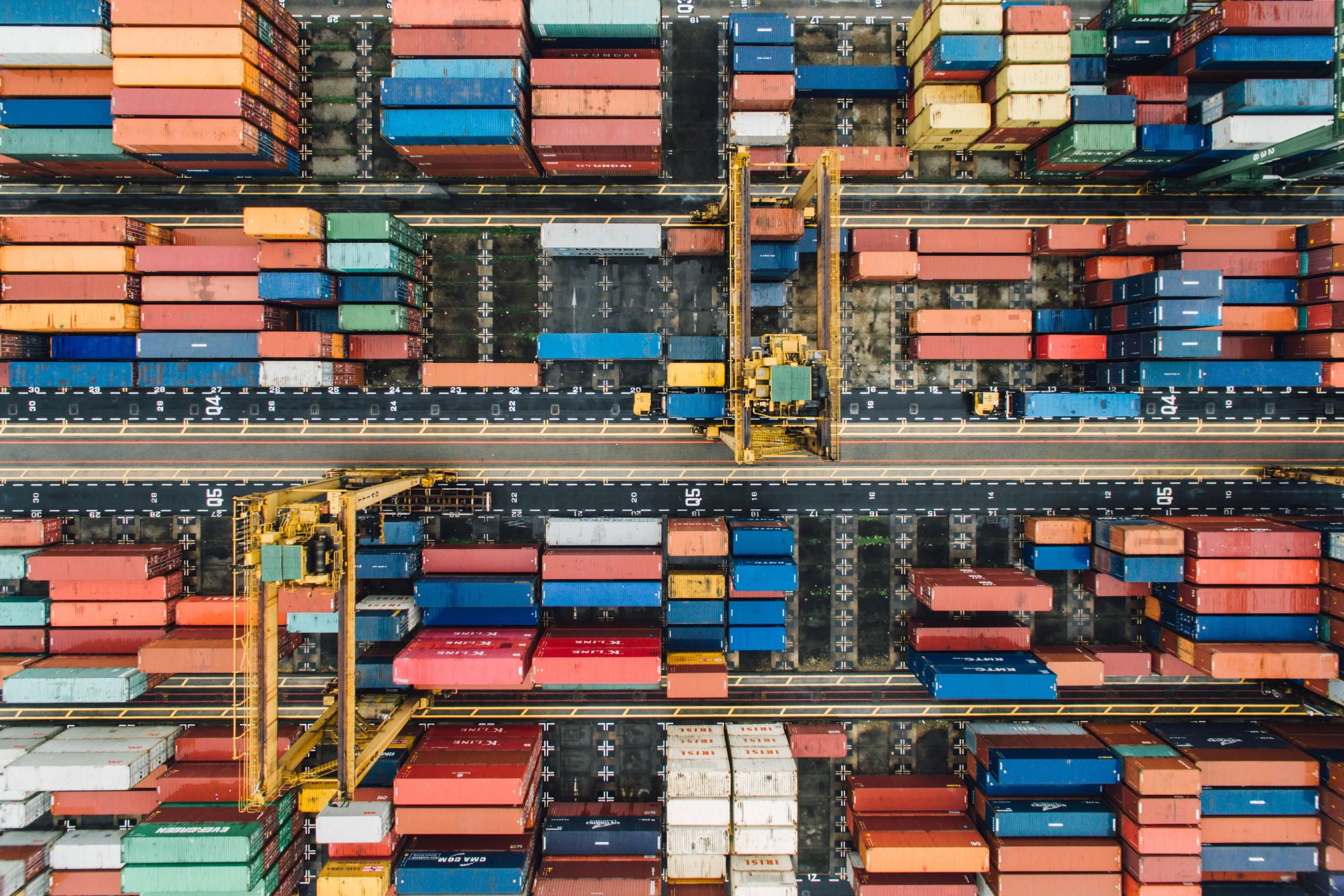
Challenges and learning from MOSOLF group's emission management project
This article summarizes key challenges and solutions in building up a sustainability function, from emission data collection to management buy-in and communication. The discussion took place at the Impact Festival 2023.
Link
During a discussion at the Impact Festival in Offenbach, Lutz Fricke, Head of Sustainability, shared his experience and learning from embarking on a climate journey at MOSOLF. Helen Tacke, the founder and CEO of Cozero, MOSOLF technology's partner, joined him on stage. This blog summarizes the key challenges and solutions in building up the sustainability function:
- Emission data collection
- Management buy-in
- Change management
- Project communication
A replay video of the 30-minute discussion in German is available below.
The project
The German automotive leading system provider MOSOLF launched a global decarbonization project to measure and reduce its emissions in collaboration with Cozero. Lutz kicked off the project with his team in 2022.
In parallel, the logistics group committed to developing sustainable practices to contribute to climate goals. In 2023, MOSOLF announced the development of its fleet of electric trucks and plans to construct a 23-hectare photovoltaic solar panel array in Baden-Württemberg. The group is also expanding its fleet with electric car transporters and charging infrastructures as part of its commitment to electromobility.
"We see these [decarbonization] efforts as necessary not only in terms of climate protection, but also as a clear competitive advantage." Lutz Fricke
During the first phase of this transformation project, Lutz and its team wanted to assess and measure the scope 1 and 2 emissions of the group logistics activities across the territory. The decision was influenced by the group's significant control over the value chain. Unlike many logistics companies that heavily depend on subcontractors, MOSOLF controls most of their operations. This unique setup made addressing scope 1 and 2 emissions a top priority for Lutz's team. A second step will be to implement accounting for scope 3 emissions and define the group's reduction goals and measures.
Data collection
With 50 physical locations, 3,000 employees, and 1,000 special vehicle transporters, collecting data could only be time-consuming and complex for Lutz's team. He reminded us how critical it was for them to obtain complete and historical data to build an exhaustive picture of the group's emissions.
The first step was to precisely inventory Scope 1 and 2 emissions. After that, the team followed a decentralized approach with local project responsibilities for data collection.
Lutz explained how engaging site managers and responsible individuals at each location in the data collection process contributed to its success:
It's important to have a structure in place. So they can say, 'I know there's someone at each location, we come together.
This approach also allows Lutz and its team to identify concrete, local improvement levers:
At the end of the day, we need a good overview of emissions in the company's different locations, broken down in a granular way so that we can answer questions like: Where are the levers? Where can I improve? Because what I'm doing now is not just optimizing my costs, or chasing my business goals, I have a third dimension. And that third dimension is ultimately sustainability performance, and passing that on.
Helen also highlighted the decentralized nature of the logistics industry and the need to work with various stakeholders at different locations. They emphasize that having intrinsically motivated contacts in the locations is crucial for driving sustainability efforts forward.
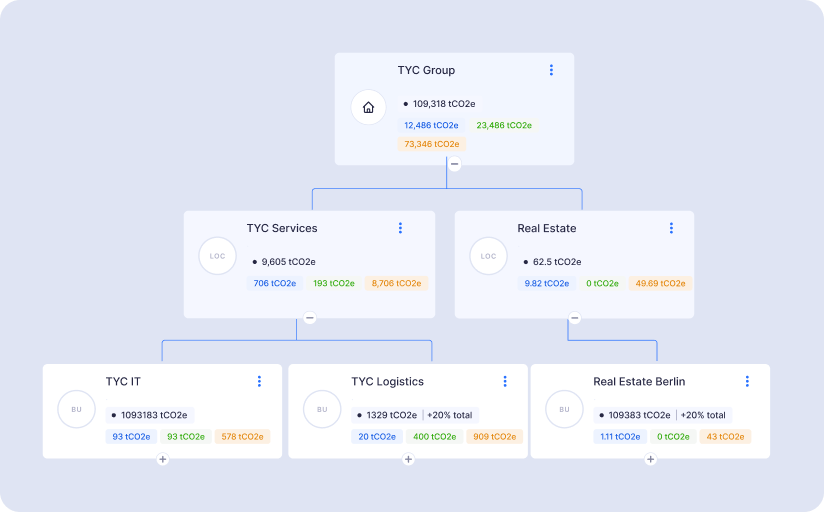
Management buy-in
Lutz explained that obtaining buy-in from top management can be challenging, especially as the project starts to scale. Therefore, one of their team's roles was to show the leadership the value of sustainability initiatives and their alignment with the business's goals.
The solution was to create a continuous bridge between financial control and climate accounting. Aligning sustainability and financial control and making a parallel between climate performance and financial performance creates a shared understanding of the benefits.
Managers have learned to focus on numbers. That's why my focus is clearly on adopting that language, speaking it, and meeting them where they stand.
For example, Lutz explained that showing the financial impact of sustainability, such as the cost savings through reduced energy consumption, helped get management on board:
It's not just about having emission number; I can allocate and break it down to a performance to then pass it on. [...] They quickly came on board, and the CEO was genuinely enthusiastic and fully supportive.
Helen emphasized the importance of having a CFO-level involvement and aligning sustainability efforts with procurement decisions and other financial aspects of the business.
Lutz added that: "the numbers, and continuous tracking are so crucial. Because showing that, ultimately, alongside financial control, there's also climate control, and it can't be a goal to let them run in parallel but to integrate them. I believe that's an important parallel process."
As Helen pointed out, the good news for logistics companies is that this process is relatively straightforward. Many optimization initiatives aimed at enhancing efficiency and saving cost, such as route optimization, naturally lead to emissions reduction as well.
Teams can quickly identify further opportunities for improvement by optimizing operational processes based on efficiency gains.
Change management and communication
While customers in the sector are pushing for more sustainability, it may not be easy to convey the need for change internally. Employees and site managers can initially be skeptical about the transformation and must be convinced of its importance.
You have to approach employees with a respect and take their fears and concerns about this change seriously. Lutz Fricke
For Lutz, there was a need to navigate change management within the organization. His solution was to visit every 40 locations and meet every responsible on-site to establish a dialog and transparent communication:
You can only bring people along if you involve them in this process. That's why this part is extremely important. We spoke to all the employees on-site who were affected. We stood in the boiler room of the farthest warehouse, smelled the oil, and I believe that's necessary.
As a result, Lutz and his team are now closely collaborating with every site during the data collection phase. They created a structure for information exchange and have open communication streams with all stakeholders:
That was probably a great motivator because they are alone at the location.
To distribute the information, they created a "hub of truth" to track and manage sustainability data internally, making it usable for various departments and processes within the company. This platform includes articles in the employee magazine and information sessions for on-site employees:
It's important that we don't just focus on one channel, but we've built an internal knowledge platform.
For Lutz and its team, the sustainability journey continues. They will finalize the data collection and gather critical stakeholders during a workshop. They'll collectively look at the analyzed data to derive and define goals to improve the sustainability performance of the MOSOLF group. Importantly, this journey continuously focuses on improving data quality as they progress.
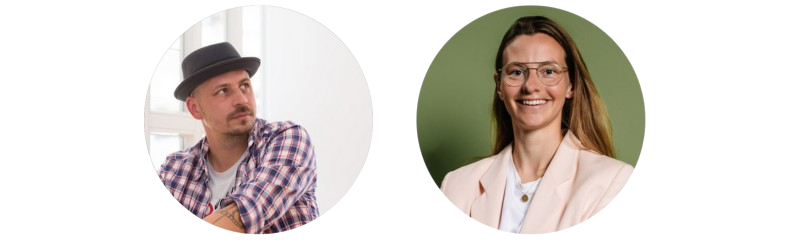
Lutz Fricke joined the MOSOLF group in 2018 as a Digitalization Project Manager after working in various roles in the media industry in Berlin and Switzerland. Since 2021, he has led the newly created Sustainability department as Head of Sustainability.
Helen Tacke is the founder & CEO of Cozero, the Berlin-based ClimateTech startup working with Mosolf. As the driving force behind Cozero, Helen is revolutionizing digital and data-driven climate controlling with a strategic and economic anchor in businesses.